Top tips: 5 use cases for digital twins in the manufacturing sector
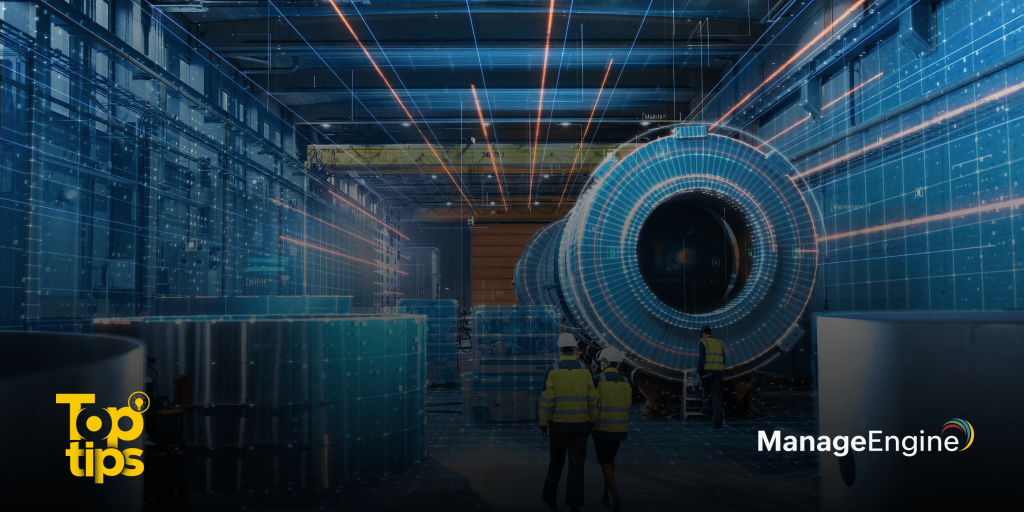
The manufacturing sector has long been at the forefront of cutting-edge innovations, from complete automation and collaborative robotics, to advanced materials and IoT. By combining key aspects of advanced manufacturing—efficient production, intelligent production, and effective organization—the manufacturing process can be revolutionized like never before. A new and notable advancement is digital twin technology. It's rare to see a form of technology that can single-handedly transform an entire sector, but that's exactly what digital twins are poised to do with manufacturing.
A single solution with multifold benefits
A digital twin is an exact virtual replica of an object, process, or system that can perfectly mimic it in both look and function. Digital twins use large amounts of real-world data and machine learning to run complex simulations on the subject accurately and in real time, without having to experiment on it physically. The benefits are multifold: you can save time, resources, and stress—nothing done to the digital twin can cause actual damage to the physical subject.
Admittedly, a digital twin is only as good as the data it has been trained on. But if you've done your part, an advanced digital twin can also be used as a substitute for a product that has already hit the market. This becomes a form of field testing where you can digitally simulate real-world use and make further improvements, while also gaining in-depth insights as to how your product performs under regular use. This can help with maintenance and time to resolution (TTR).
How do digital twins fare in the real world?
Here are five real-world uses cases for digital twins that underline their importance in the manufacturing sector.
1. Risk assessment
Digital twins add another layer of scope and accuracy to your risk assessment. With digital twins, you can test out likely failure scenarios to see how your product will perform under various conditions. These tests can make your product safer to use and even ensure that the build quality complies with the relevant regulations. Ultimately, digital twins enable you to detect, forecast, and prepare for more risks than traditional risk assessment methods.
2. Research and development
Digital twins can assist organizations in the R&D phase of a product's life cycle.
Using either data from real-life examples or hand-crafted data sets and parameters, organizations can first determine the viability of a product concept. They can then create accurate prototypes that perfectly capture how the product will perform in real-life usage conditions.
For instance, once an organization has identified a need in the market, it can create a virtual representation of a product, built on an extensive set of usage conditions, that can be tested using historical data as to whether it does indeed fulfill that particular need. Once this has been confirmed, the organization can then create a prototype for further testing.
3. Product testing
Using digital twins for product testing works very similarly to R&D, the only major difference being the end goal: viability versus quality. After an organization has tested the viability of the product in the market, it can perform further testing for quality.
Historically, simulations have always been the best way to gauge how a product will perform in various conditions. Digital twins are like simulations, only much more layered and complex, enabling you to test out many more variables than you could with traditional simulations. By using this technology, engineers can test whether the product will work as expected, as well as its quality and safety, even before they begin building the physical prototype.
4. Predictive maintenance
Digital twins can use their powerful machine-learning models, which can make complex calculations using historical data and trends, to predict when a failure may occur. These predictive capabilities are being leveraged by organizations to accurately plan for and schedule maintenance tasks for the object before the predicted malfunction, which can reduce downtime significantly. While they are not foolproof, there are already cases of digital twins helping with predictive maintenance. For example, General Electric uses the insights derived from testing digital twins of its wind turbines in a wide range of conditions to detect issues and resolve them before outages are caused.
5. Manufacturing infrastructure monitoring
The scope of digital twins is not just limited to the output of a manufacturing firm; it can also apply to the manufacturing infrastructure itself. An organization can use digital twins to derive real-time insights relating to the manufacturing process to find any existing or potential problem areas or even key areas of improvement, which can result in an overall more streamlined and well-optimized end-to-end production process.
Digital twins are, no doubt, going to transform the manufacturing sector from top to bottom. Their applications are numerous and not just limited to manufacturing alone. Digital twins can play a vital role throughout the entire product lifecycle management (PLM) process. And even though this tech is still new, you shouldn't write it off as a passing fad. With digital twin technology, the manufacturing industry is at the cusp of something huge.